针对立磨磨辊轴承在使用过程中时常会损坏的问题,文章结合某水泥厂的实际案例,通过对油品品质、设备本体、油站和操作等方面进行分析,结合油品检测等技术手段,找到损坏原因并给出改进措施,提供了此类问题的解决思路。
关键词:立磨;轴承损坏;解决思路
立磨磨辊部件是立磨粉磨的关键部件,其运行状态的好坏直接关系到生产的安全运行以及生产效率的高低,尤其对水泥矿粉等企业节约运行维护成本起着关键作用。
由我公司供货的某水泥厂立磨于2017年10月投入使用,2018年6月发现磨机振动偏大、产量降低、运行工况较差,停机检查过程中发现磨辊轴承盘动困难。专业技术人员对磨辊轴承进行检查发现,有2套磨辊轴承出现损伤,借助专业工具检查后,发现轴承出现剥落、掉块等现象,于是安排返厂进行进一步分析检查。
1 失效件拆解分析
通过对失效的磨辊拆解检查发现,圆柱轴承与圆锥轴承均出现不同程度的损坏,主要表现为以下几个方面:(1)圆柱轴承、圆锥轴承滚动体表面点蚀(锈蚀)严重,局部有剥落;(2)圆锥轴承外圈滚道面碳化发黑,剥落严重;(3)圆锥轴承保持架局部变形严重,局部掉块,个别滚动体脱离保持架;(4)圆柱轴承有2个滚动体碎裂。
2 轴承损坏的原因
磨辊是立磨的核心部件,而轴承则是核心部件的心脏,轴承的正常工作是磨辊可靠运行的关键。磨辊轴承是在高温、冲击、低速、重载的复杂工况下运行的,外部有高温粉尘的恶劣环境。基于此,磨辊轴承一般选择知名品牌的
进口轴承,满足设计寿命在80000h以上,正常使用寿命保证50000h以上。
磨辊轴承在短时间出现损坏,需要认真分析轴承损坏原因,利于彻底解决问题,化解客户疑虑及判断事故责任。
2.1 润滑不良
磨辊轴承润滑是通过集中润滑系统来实现的,通过稀油站向磨辊内部供油,油品为460#极压工业齿轮油。磨辊装置结构及润滑油走向如图1所示。
图1 磨辊装置结构
现场检查发现,磨辊腔体内部油品发黑、油品黏度较低,现场对油品取样进行分析,结果如表1所示。由表1可以看出,该牌号油品40 ℃正常的运动黏度应该在460mm2/s,实测值为287.7mm2/s,水分超标,润滑油本身碳化严重,品质下降,铁与锌杂质含量增加。从分析结果判断,该型立磨使用的油品已不满足磨辊轴承正常运行所需要的油品条件。
表1 油品分析结果
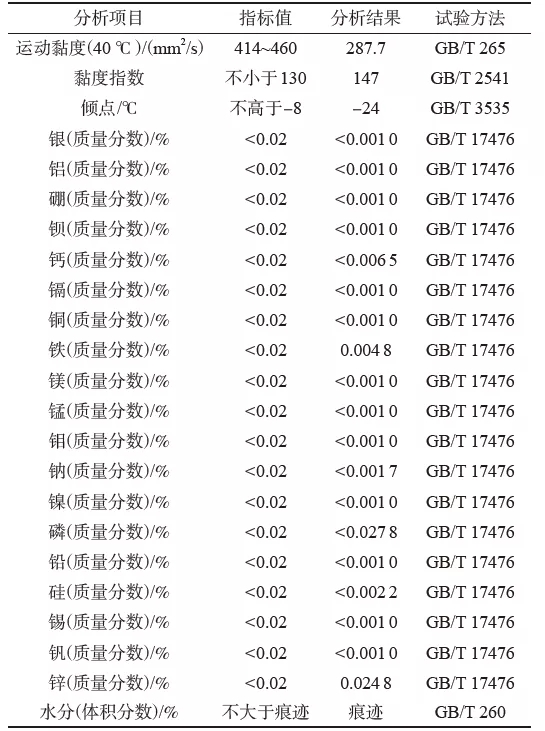
2.2 现场操作维护不当
立磨润滑系统原理如图2所示,磨辊润滑系统工作原理为:润滑系统工作时,油液经供油泵从油箱抽出,经过滤器、冷却器、分流器等进入磨辊内部,经循环润滑换热后,由回油泵从磨内强制抽出,送回油箱,润滑系统通过循环往复实现磨辊的润滑功能。单个磨辊供油泵分配流量为13 L/min,单辊配置一个能力为20 L/min的回油泵强制回油。
图2 磨辊润滑系统原理
正常工作时磨辊的回油温度一般比环境温度高30~50 ℃,中控联锁设置回油温度要求75 ℃报警,85 ℃停主机。正常情况下停磨4~6 h后打开磨门,停机后拆开磨辊后端盖检查内部轴承,轴承温度应在70~90 ℃,该项目磨辊内轴承温度约为120 ℃。
中控记录显示在轴承损坏前2周回油温度长时间基本接近环境温度,中控人员未重视该异常情况,也未把该异常情况及时通知现场人员进行检查,同时现场维护人员也未对润滑系统供、回油情况等进行定期检查。经复查,损坏磨辊对应的润滑油站供油阀门开度较低,单独开启油站验证,该磨辊后端测试供油量约为0.5 L/min,远远低于正常要求。
从2017年10月投产以来,磨辊润滑油站从未更换过油站滤芯,拆下检查发现滤芯金属泥较多,油品中的杂质也会导致轴承损伤。
以上现象说明由于操作人员维护不当或者不及时,致使磨辊内部供油不足,导致磨辊内部热量无法及时带出,润滑油黏度下降较多,无法正常形成润滑油膜,使磨辊内部润滑工况恶劣,连续运转导致轴承损伤或损坏。
2.3 油封失效
检查发现磨辊油封处有漏油现象,根据磨辊油封设计原则,漏油表明磨辊内部油封损坏,但因磨辊本身还有2道防尘密封,防止外界物料等细小杂物进入损坏轴承,故暂时无法判断是否有粉料等杂物进入轴承。
拆卸检查,发现磨辊防油密封损伤,橡胶部位有划伤,密封唇口无物料等杂物,说明油封防油功能虽然失效,导致磨辊部分有漏油,但防尘功能正常,无金属、粉料颗粒进入磨辊轴承内部影响轴承正常运转,基本排除油封失效造成轴承损伤。
2.4 轴承本身质量问题
通过查验轴承原始制造记录,轴承出厂前热处理、尺寸等相关检验数据合格,同时通过核对同型号的同批次轴承,均未出现上述情况的损伤。进一步对失效轴承硬度、化学成分与金相进行了分析。
(1)硬度分析结果为59.5~59.7HRC,符合订货要求中对轴承材质的要求。
(2)化学成分结果见表2,结果符合订货要求中对轴承钢100CrMnMoSi8-4-6的要求。

(3)金相分析结果显示,轴承材质中未发现屈氏体,符合订货要求中对材质的热处理要求。
上述结果说明,轴承本身不存在缺陷,轴承损伤与轴承本身无关。
2.5 装配问题
按照磨辊出厂编号,查验相关部件的尺寸记录,符合图纸设计要求,磨辊*终装配记录符合磨辊安装指导步骤要求,出厂游隙符合要求。
结合轴承损坏现象,通过分析可知,现场人员操作维护不当,加之润滑油品质低,造成润滑不良,是导致轴承损坏的主要原因。
3 改进措施
结合损坏结果与原因分析,为保证该厂后续持续正常生产,从以下几个方面改进:
(1)拆卸完毕后,对所有部件进行清洗,然后严格按照设计图纸复检相关尺寸,保证所有部件符合出厂要求。
(2)对轴承等损伤部件更换,并对相关关键尺寸进行检查,保证符合使用要求。
(3)严格按照新产品出厂要求,装配相关部件,控制磨辊轴承出厂游隙。
(4)发货前磨辊内部灌装防锈油,保护轴承防止锈蚀。
(5)将原磨辊润滑油站中的润滑油全部排出,并且清洗所有磨辊润滑相关管路,保证管路内部清洁,无金属杂质、无水锈,然后检测相关泵组的供回油能力、温控系统的灵敏度与精度等。
(6)磨辊发往现场后,派出专业人员安装磨辊,调试油站,保证轴承供油充足,检查磨辊内润滑与轴承运转情况。
(7)从生产维护、故障判断、油品选择、油品检测等角度对企业员工进行免费的技术指导与培训,杜绝该类事件的再次发生。
4 结束语
企业在生产设备出现故障时,往往首先从加工精度、安装等机械方面找原因,特别是在轴承、齿轮等关键部件出现损坏时,会直接怀疑设备本身质量问题,而很少从润滑方面进行分析,往往导致不能有效解决问题或不能从根本上解决问题,造成额外的附加经济损失。企业在设备维护管理中,应将润滑维护管理作为重点。润滑维护管理是一套完整体系,主要包括润滑剂选择、润滑方式、润滑操作、润滑检测分析和润滑剂管理五个方面,环环相扣,缺一不可。